From soft fabrics to solid walls: FabBRICK reinvents construction materials with recycled textile waste
French architect Clarisse Merlet and her studio show the potential of recycling textiles to create construction materials through FabBRICK

“We are a design agency specialising in Research and Development of an eco-designed material. The idea is to recycle discarded textile into an insulating, structural and aesthetic building material. We can use the brick to make furniture or partition walls” explains Clarisse Merlet, architect and founder of FabBRICK.
She is demonstrating since 2019 the potential of waste coming from the textile industry, turning it into proper construction material with both reliable technical performance and a unique visual appeal.
The young architect started developing her idea while she was studying, first as a school project, before she realized the full potential of it:

“When I was studying architecture, I felt concerned about the issue of the pollution in the construction industry. I started making bricks with waste from plastic bottles, cardboard and then finally textile because the fashion industry is one of the most polluting industries.”
As a matter of fact, the annual waste from the textile industry represents not less than 4 million tons of clothes only in Europe. If the idea of Clarisse can seem optimistic on paper, the numbers are speaking for themselves.
There are some great business opportunities for anyone finding how to reuse this textile, especially in France where only 32.5% of clothes in the market are gathered by collecting agencies every year.

In order to bring her idea to life, Clarisse and her team had to experiment with different techniques before finding the process that would be used to produce the bricks.
“The textile is being compressed in a mould. To reach a good result, we need to use a crusher to transform the textile into fibers and little pieces of fabrics.
Then these fibers are mixed with a binding, resulting in a [material similar to] clay that will be shaped by the mould” she explains.
[ Find out more about designers using waste to create amazing products, don’t miss Teun Zwets made a funky planter out of his own trash ]
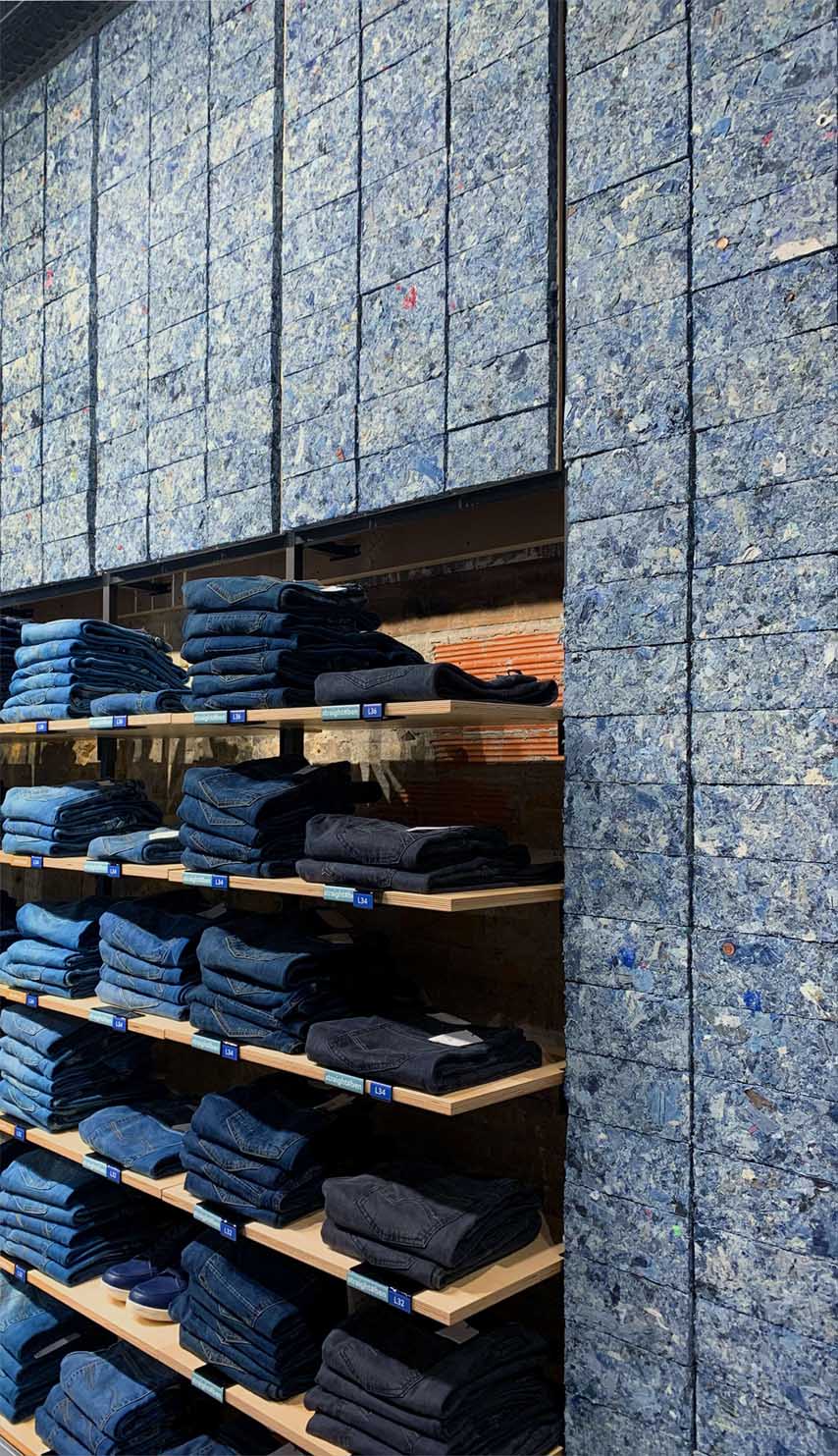
Going deeper into details, Clarisse agreed to share with us the different stages the brick goes through, from discarded clothes to being used as construction material for the different projects they work in collaboration with.
The steps are:
- Step 1: We only accept discarded clothes. We receive them in our studio in Paris sorted by colors.
- Step 2: For each project, the customer chooses the format (we have developed around 10 different sizes) and the color. We don’t dye our bricks, the color is obtained by the textile we use.
- Step 3: Shred the textile to obtain fibers. We can obtain 3 different shapes of fibers. 7mm, 20mm and 40mm. We pick the size depending on the project.
- Step 4: Make the glue. The glue is 100% made of ecological ingredients, we don’t use any chemicals for it.
- Step 5: Mix the glue and the fibers by hand. We weigh the mixture to make sure each brick has the same density.
- Step 6: Incorporate the mixture by hand in our patented machine.
- Step 7: Action the machine in order to compress the mixture inside the mould. It takes 30min to shape the mixture into a brick.
- Step 8: The brick dries in ambient air between 10/15 days.
- Step 9: We can use these bricks to create furniture and partition walls too.
- Step 10: We can send just the brick as a unit to the customers or as a product (chair, table, etc..)”.
Behind this simple manufacturing process lays a tremendous amount of work in research and development to reach this result.
The glue used to bind together the textile fibers was developed with an engineer who is one of the first employees to join the studio.
“The ingredients used for our glue are secret but 100% ecological. The hardest part of the research was to make an ecological glue rot-proof, that doesn’t develop molds.”
Thanks to these innovations, the end product is a brick with very impressive characteristics.
“The brick has a very good mechanical resistance almost like a concrete block. This is why the structure of our furniture/ partition walls is made directly with our bricks. On another note, it has a good insulating quality, acoustic and thermal, and a good resistance to fire. Hence we can make panels that improve the ambiance of a room or a public space. It also has a good water resistance but we recommend indoor use for now.”
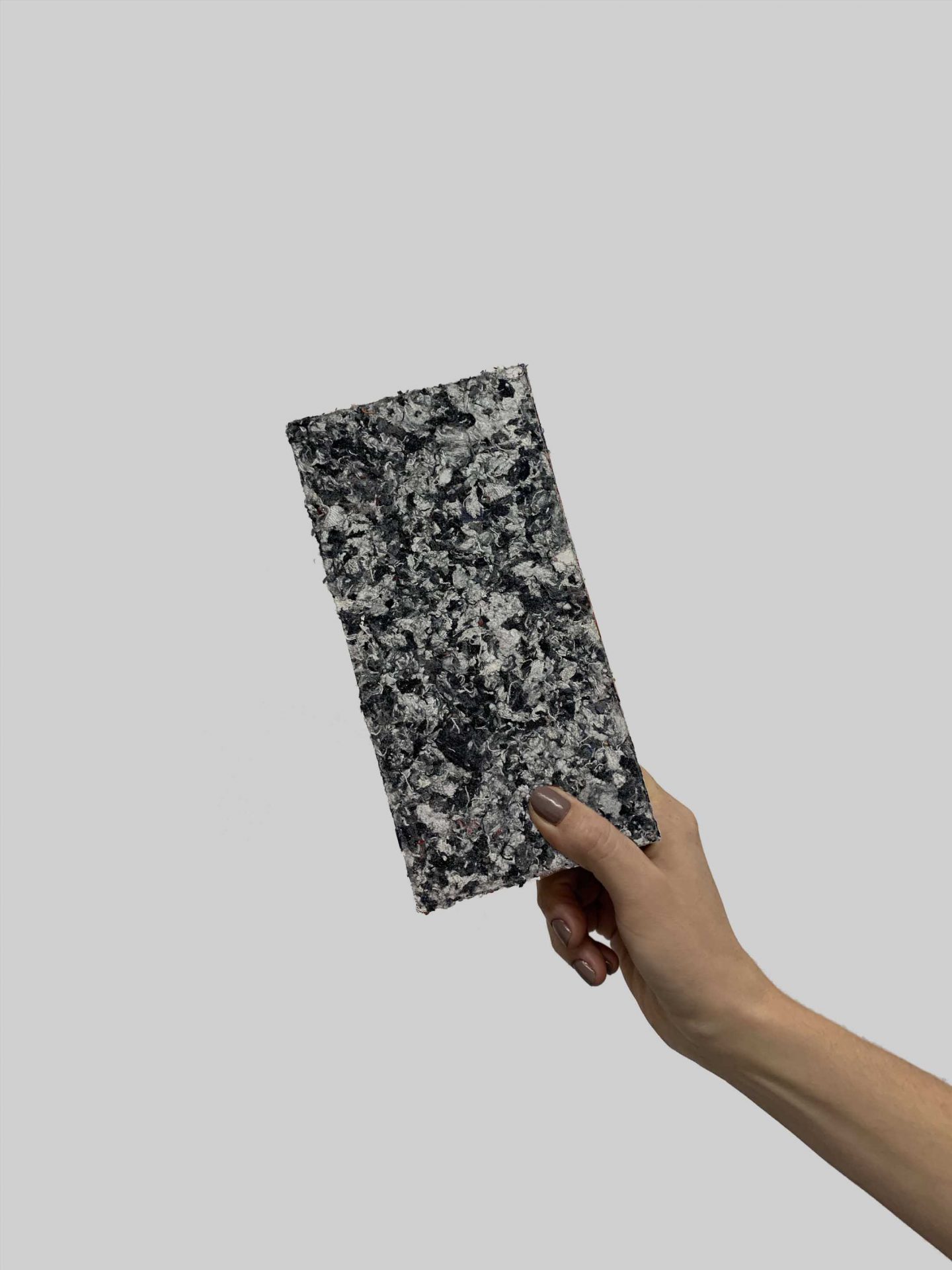
But more than a simple design studio, FabBRICK wants to reconnect with local manufacturers and promote trade of proximity.
“At FabBRICK having a local production is at our core value and DNA. Even when it comes to our ingredients, machines and everything we use here. Local design production is possible, and we can do everything locally, just need to adjust and organise.”
Promoting local production doesn’t mean that the concept is exclusive to France.
On the contrary, the studio envisions the possibility of a worldwide expansion, promoting local trade through a global vision.

“FabBRICK can be developed worldwide, the reason being that unfortunately, fast fashion is everywhere, so we can always be close to a source of textile waste.”
The next step is to [automate] the production so that we can recycle even more. At the moment the process is artisanal, the machines are manually operated.
To start, duplicate our model locally in France then export globally the FabBRICK Factory.”
[ Curious to know about other products made out of recycled waste? Don’t miss Studio ThusThat’s lamp made from waste products from copper ]